talk about fpc connector product knowledge and structure
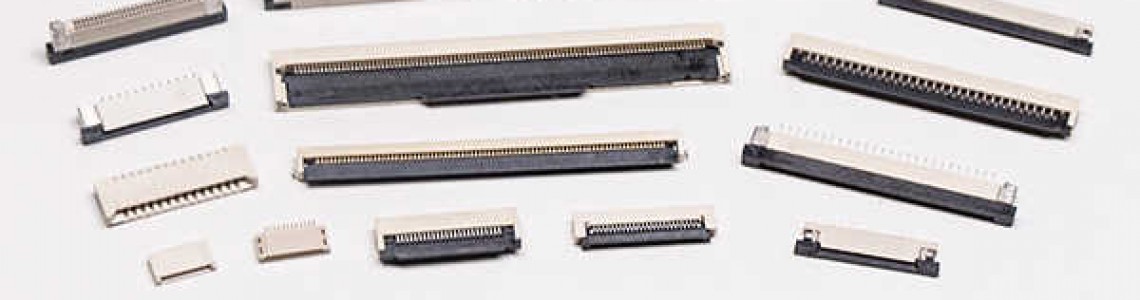
"talk about fpc connector product knowledge explanation and structure composition" is organized by cyberebee for you, purchase connectors, and on cyberebee . nowadays, with the popularization of smt technology in the field of electronic products, the application of surface mount connectors is becoming more and more widespread. , various types of pcbs have corresponding surface-mount connectors. from the through-hole (t / h) soldering process to the surface-mount (smt) soldering process, the terminal arrangement pitch of the connector is gradually reduced to 0.8mm and 0.5mm, and the application of the smt process allows the pcb to be double-sided. welding electronic components has greatly increased the density of components on the pcb. various types of consumer electronics products have now been combined with miniaturization, thinness, and high performance. the use of flexible printed circuit boards (fpc) and matching fpc connectors to reduce space, weight, and assembly costs has been achieved. accepted by many customers.
first, the role and application of fpc connector products
fpc connector products are used to connect circuit boards (pcb) and flexible printed circuit boards (fpc) to achieve mechanical and electrical connection. today's fpc connectors are mainly used in electronic devices such as lcd and led liquid crystal displays, scanners, digital cameras, game consoles, tablet computers, notebook computers, and car theaters. fpc connector products are also widely used in audio, digital computers, camcorders, car stereos, televisions, typewriters, calculators, cash registers, telephones, cd-roms, vcds, dvds, copiers, printers, wireless instruments and other equipment.
structure and composition of fpc connector products
the fpc connector can be reduced in thickness, and in order to suppress the area occupied by the connector, it is a connector that seeks miniaturization and high-frequency signal transmission. this connector consists of four parts, namely a rubber core, a tongue, a terminal, and a soldering piece. the following is the explanation of the knowledge of these four parts;
1. the function of the fpc connector rubber core is to protect the terminals, insulation, guide the connection, provide the strength of the mechanism, etc. the manufacturing process of the fpc connector rubber core generally uses injection molding technology, and the material is mostly pa9t material.
the plastic body of the plastic core of the fpc connector is an equally-spaced sheet-like barrier structure, which allows the terminals to maintain a small-pitch arrangement and provide a certain holding force after assembly. according to the requirements of the product, the plastic body must have sufficient strength and toughness, and there must be no warping deformation before and after smt welding. in order to meet the requirements of the smt manufacturing process, the terminal soldering area of the entire product is strictly required to have good flatness and coplanarity. generally, the industry standard is coplanarity 0.10max, otherwise it will cause poor soldering with pcb and affect the product. use.
2. the function of fpc connector tongue is crimping cable, insulation, guiding when connecting, providing mechanical strength, etc. the manufacturing process of fpc connector tongue is generally using injection molding process, the material is pa10t, pps material.
the tongue piece parts of the fpc connector are matched with the plastic body. after the fpc is inserted, the tongue piece parts are used to lock the fpc to maintain a certain contact force, so the parts are required to have sufficient rigidity.
3. the function of the fpc connector terminal is the transmission of the conductor of electronic signals. the manufacturing process is stamping + electroplating (gold or tin plating to improve the welding ability of the product). the material is phosphor bronze c5191.
generally, there are two ways for the design of the terminal structure, one is a punching plane blanking terminal (abbreviated as a blanking terminal), and the other is a bent and formed terminal (abbreviated as a formed terminal) after punching. due to the need for sufficient elasticity and relatively complex shapes of narrow-sheet female terminals, if stamping is used, it will cause difficulties in stamping and the size and accuracy of the molding are not easy to control. therefore, female terminals are usually molded.
4. the function of fpc connector welding piece is component positioning, fixing, increasing strength, etc. the manufacturing process also uses stamping + electroplating process (gold or tin plating to improve the welding ability of the product), and the material is bronze c2680.
the soldering sheet is used to strengthen the connection between the connector and the pcb, and can avoid damage to the soldering of the terminal and the pcb due to excessive stress on the terminal. after assembly, the soldering piece must be consistent with the coplanarity of all the terminals. in fpc connectors with fewer pins, the soldering piece is not a mandatory part.
Leave a Comment