why do we need an ultrasonic module, and how to set everything ready?
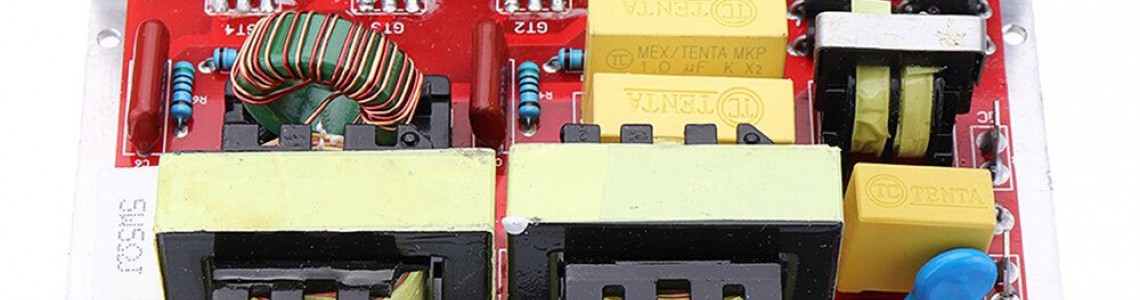
why do we need an ultrasonic module, and how to set everything ready?
sound wave is the propagation form of sound. sound wave is a kind of mechanical wave, which is generated by the vibration of sound source. the frequency of sound wave that can be heard by the human ear is generally between 20hz (hertz) and 20khz.
sound begins with the vibration of air particles that together push adjacent air molecules, slightly increasing air pressure. the air molecules under pressure then push the surrounding air molecules, which in turn push the next set of molecules, and so on. as areas of high pressure pass through the air, they leave areas of low pressure behind. when these changes in pressure waves reach the human ear, they vibrate the nerve endings in the ear, and we hear these vibrations as sound.
sound waves travel at significantly different speeds in different media - alchetron, the free social encyclopedia
air: the speed of sound waves at normal temperature and pressure is 344m/s
fresh water: 1430m/s
seawater: 1500m/s
steel: 5800m/s
aluminum: 6400m/s
quartz glass: 5370m/s
rubber: 30-50m/s.
the temperature and pressure of the medium change, and the speed of sound also changes. the normal temperature usually refers to the temperature at 20°c. when the temperature drops to zero, the speed of sound waves in the air will be 331.5m/s, and the speed of sound will increase by 0.607m/s for every 1°c increase in temperature.
depending on the frequency of the sound wave, it can be divided into the following categories
sound waves with a frequency lower than 20hz are called infrasound or ultra-low sound;
sound waves with a frequency of 20hz~20khz are called audible sound;
sound waves with a frequency of 20khz~1ghz are called ultrasonic waves;
sound waves with a frequency greater than 1 ghz are called ultrasonography or microwave ultrasound.
ultrasound is a mechanical wave with a very short wavelength
transverse wave, poor diffraction ability, good anisotropy, easy to scatter. it must rely on the medium to propagate and cannot propagate in a vacuum. it can be used for cleaning, crushing stones, sterilization and disinfection, etc.
transverse wave - s wave:
the direction of wave propagation is perpendicular to the vibration direction of the particle
transmissible in solid
non-transmissible in gases and liquids
sound does not travel in gases and liquids
longitudinal wave - p wave:
the wave propagates in the same direction as the particle vibrates:
transmissible in solid
transmissible in gases and liquids
sound wave is a mechanical wave, transverse wave, which obeys the principle of conservation of mechanical energy. ultrasonic waves are no exception. the propagation of ultrasonic waves depends on elastic media. when propagating, the particles in the elastic media are made to oscillate, and energy is transmitted through the media in the direction of ultrasonic waves.
due to the compressibility of gas and liquid, transverse waves cannot propagate in gas and liquid. sound wave is a kind of mechanical energy, energy is conserved, but it cannot be propagated, what should we do? is it suffocated, no.
sound waves will cause particle vibration in the liquid, and the acceleration of particle vibration is proportional to the square of the ultrasonic frequency. if it is ultrasonic waves, it will generate a great force. when strong ultrasonic waves propagate in liquid, due to nonlinear effects, acoustic cavitation will occur. .
the shock wave emitted by ultrasound when the cavitation bubble suddenly closes can generate thousands of atmospheric pressure around it, and the direct and repeated impact on the dirt layer will destroy the adsorption of the dirt and the surface of the cleaning part on the one hand, and cause the dirt on the other hand. the destruction of the layer breaks away from the surface of the cleaning parts and disperses them into the cleaning solution. the vibration of the air bubbles also scrubs solid surfaces. the air bubbles can also "drill" into the cracks to vibrate and make the dirt fall off. for greasy dirt, due to ultrasonic cavitation, the two liquids quickly disperse and emulsify at the interface. when the solid particles are wrapped in oil and adhere to the surface of the cleaning piece, the oil is emulsified and the solid particles fall off. the cavitation bubbles will cause the liquid itself to circulate during the vibration process, which is the so-called acoustic flow. it can cause a high velocity gradient and viscous stress on the surface of the vibrating bubble to promote the destruction and shedding of the dirt on the surface of the cleaning part. the high-speed micro-jet generated by ultrasonic cavitation on the surface of solid and liquid can remove or weaken the boundary dirt layer , corrode the solid surface, increase the stirring effect, accelerate the dissolution of soluble dirt, and strengthen the cleaning effect of chemical cleaning agents. in addition, ultrasonic vibration causes a large vibration velocity and acceleration of particles in the cleaning liquid, and also makes the dirt on the surface of the cleaning parts subject to frequent and intense impacts. to put it simply, friends who have pets know that, for example, puppies must be dried and dried quickly after taking a bath before they can be pulled into the room. what happens if you don't dry it off? the dog will shake all over, and then the water will splatter all over the room. ultrasonic cleaning is a similar mechanism.
ultrasonic cleaning (ultrasonic cleaning) is to use the cavitation effect, acceleration effect and direct flow effect of ultrasonic waves in the liquid to directly and indirectly affect the liquid and dirt, so that the dirt layer is dispersed, emulsified and peeled off to achieve the purpose of cleaning.
the actual cleaning process in the semiconductor industry usually uses a variety of cleaning media, such as: various chemicals and deionized water, etc., and also uses various cleaning methods: rca cleaning method, dilution chemical method, imec cleaning method, single wafer cleaning and many more
what to clean and how to clean
particles,
the particles are mainly some polymers, resists and etching impurities. usually particles adhere to the silicon surface, affecting the formation of geometric features and electrical characteristics in the next process. according to the analysis of the adhesion between the particles and the surface, although the adhesion force shows diversification, it is mainly van der waals attraction, so the removal method of the particles is mainly to undercut the particles by physical or chemical methods, gradually reduces the particle's contact area with the silicon surface and eventually removes it.
organic matter
organic impurities exist in various forms in the ic manufacturing process, such as human skin oil, clean room air, mechanical oil, silicone resin vacuum grease, photoresist, cleaning solvent, etc. each kind of pollutant has a different degree of influence on the ic process, and usually forms an organic film on the wafer surface to prevent the cleaning solution from reaching the wafer surface. therefore, the removal of organic matter is often carried out in the first step of the cleaning process.
metal contaminants
in the ic circuit manufacturing process, metal interconnection materials are used to connect individual devices. first, contact windows are made on the insulating layer by photolithography and etching, and then metal interconnection is formed by evaporation, sputtering or chemical vapor deposition (cvd). interconnect films, such as al-si, cu, etc., are etched to produce interconnect lines, and then chemical mechanical polishing (cmp) is performed on the deposited dielectric layer. this process is also a potential pollution process for the ic manufacturing process. while forming metal interconnections, various metal pollutions are also generated. appropriate measures must be taken to remove metal contamination.
native oxides and chemical oxides
silicon atoms are very easy to oxidize to form an oxide layer in an environment containing oxygen and water, which is called a native oxide layer. after the silicon wafer is cleaned by sc-1 and sc-2 solutions, a chemical oxide layer will be formed on the surface of the wafer due to the strong oxidizing power of hydrogen peroxide. in order to ensure the quality of the gate oxide layer, this surface oxide layer must be removed after wafer cleaning. in addition, oxides such as silicon nitride and silicon dioxide deposited by chemical vapor deposition (cvd) in the ic process must also be selectively removed in the corresponding cleaning process.
build your own ultrasonic wash tank today with cyberebee module
Leave a Comment